The Ultimate Guide to Welding Equipment: Tools and Techniques Explained
Welding equipment plays a crucial role in various industries, enabling the joining of materials through heat and pressure. This comprehensive guide explores the types of welding equipment available, their applications, and essential considerations for choosing the right tools for your projects.
What are the main types of welding equipment?
Welding equipment includes several main types:
- Welding Machines: These devices generate the necessary heat and electrical current for welding.
- Welding Torches: Connected to the welding machine, torches direct the flame or arc onto the workpiece.
- Protective Gear: Essential for safety, including helmets, gloves, and aprons.
- Consumables: Electrodes, filler metals, and shielding gases are vital consumables.
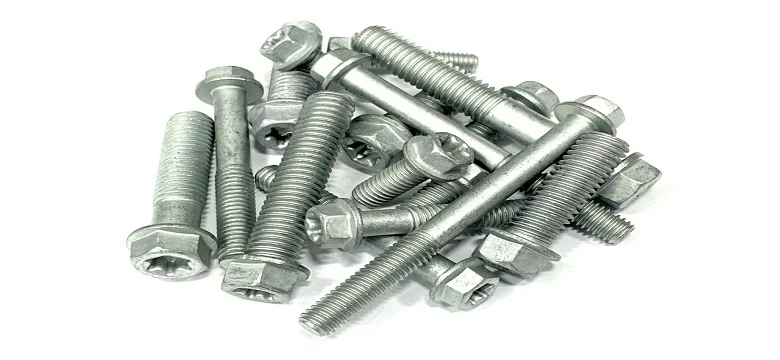
How does welding equipment work?
- Welding Machines: They convert electricity into heat to melt metal pieces together.
- Welding Torches: Direct a controlled stream of gas and filler material (if needed) to create a weld.
- Protective Gear: Shields welders from sparks, UV rays, and heat, ensuring safety.
What are the key factors to consider when choosing welding equipment?
- Project Requirements: Different projects may require specific types of welding processes (e.g., MIG, TIG, or arc welding).
- Material Compatibility: Ensure the equipment is suitable for the materials being welded (e.g., steel, aluminum, etc.).
- Power Supply: Consider whether the equipment requires electricity, gas, or both.
- Safety Features: Look for equipment with built-in safety measures to protect operators.
How can welding equipment improve efficiency and quality in projects?
- Precision and Control: Modern welding equipment offers precise control over heat and welding parameters, ensuring consistent results.
- Versatility: Different types of welding equipment cater to various welding techniques and materials, enhancing project flexibility.
- Productivity: Efficient welding equipment speeds up production times and reduces downtime, boosting overall project efficiency.
Geotextile materials are increasingly used in welding applications, particularly in construction and environmental engineering. Welding equipment can be adapted to join geotextile materials, providing durable and secure seams for applications such as soil stabilization, drainage systems, and erosion control.
Choosing the right welding equipment is crucial for achieving high-quality welds efficiently and safely. By understanding the types of equipment available, how they work, and key considerations for selection, professionals can optimize their welding processes for various projects. Incorporating advancements like geotextile welding further expands the applications and benefits of welding equipment across diverse industries.